Sering kali masyarakat awam salah kaprah dengan istilah besi dengan baja.
Apakah yang dimaksud dengan baja ?
Baja merupakan perpaduan atara besi (Fe) dan Carbon (C), Besi adalah elemen metal dan Carbon adalah elemen non metal.
Baja sendiri digolongkan menjadi dua golongan yaitu baja bukan paduan ( yang hanya terpadu dengan Carbon saja ) dan baja paduan yaitu yang terpadu dengan elemen – elemen lain sesuai dengan kebutuhan dan sifat yang dikehendaki. Elemen paduan yang ditambahkan itu sendiri terdiri dari Mangan, Chrome, Nickel, Wolfram, Silisium, dan lainnya.
Besi Carbide/ Carbon juga dinamakan Zementit. Prosentase Jumlah karbon yang ada di besi sangat berpengaruh juga terhadap kekerasan dari baja itu sendiri.
• Dengan naiknya kadar karbon (%C), maka bertambah besarlah flek hitam ( Flek-perlit ) dan bersama itu berkuranglah flek putih ( Ferrit atau besi murni )
• Pada kadar karbon mencapai 0.85%, maka besi dalam keadaan jenuh terhadap karbon. Struktur tersebut dinamakan Perlit Lamelar, yaitu campuran yang sangat halus yang berbentuk batang kristal. Campuran kristal tersebut terdiri dari Ferrit dan Zementit.
• Jika kadar karbon bertambah besar, zementit akan berkurang dan flek perlit akan bertambah. Kadar jenuh karbon sebesar 0.85% yang berdampak bertambah juga kekerasan dari baja.

BAJA KARBON
Yang dimaksud dengan baja karbon adalah baja yang hanya terdiri dari besi ( Fe ) dan karbon ( C ) saja tanpa adanya bahan pemadu dan unsure lain yang kadang terdapat pada baja karbon seperti Si, Mn, P, P hanyalah dengan prosentase yang sangat kecil yang biasa dinamakan impurities. Pengaruh dari unsure diatas adalah sebagai berikut : 1. Si dan Mn
Biasanya kandungan paling banyak untuk Si adalah 0.4 % dan untuk Mn adalah 0.5 – 0.8 %.
Kedua unsur ini tidak banyak berarti pengaruhnya terhadap sifat mekanik dari baja. Mn dipakai untuk mengurangi sifat rapuh panas dan mampu menghilangkan lubang-lubang pada saat proses penuangan/pembuatan baja. 2. Phosphor
Phosphor dalam baja karbon akan mengakibatkan kerapuhan dalam keadaan dingin. Semakin besar prosentase phosphor semakin tinggi batas tegangan tariknya, tetapi impact strength dan ductility nya turun. Prosentase phosphor pada baja paling tinggi 0.08 %, tetapi pada baja karbon rendah prosentasenya 0.15 – 0.20 % untuk memperbaiki sifat mach inability nya yaitu supaya chips/tatal yang terjadi tidak sambung-menyambung melainkan dapat putus-putus. 3. Sulfur
Prosentasi sulfur pada baja karbon 0.04 %. Sulfur dapat mempengaruhi sifat rapuh – panas.
Baja Karbon berdasarkan prosentase kadar karbonnya dikelompokkan menjadi 3 Macam. a. Baja Karbon Rendah.
Kandungan karbon pada baja ini antara 0.10 sampai 0.25 % .
Karena kadar karbon yang sangat rendah maka baja ini lunak dan tentu saja tidak dapat dikeraskan, dapat ditempa, dituang, mudah dilas dan dapat dikeraskan permukaannya ( case hardening )
Baja dengan prosentase karbon dibawah 0.15 % memiliki sifat mach ability yang rendah dan biasanya digunakan untuk konstruksi jembatan, bangunan, dan lainnya. b. Baja Karbon Menengah
Kandungan karbon pada baja ini antara 0.25 sampai 0.55 % .
Baja jenis ini dapat dikeraskan dan di tempering, dapat dilas dan mudah dikerjakan pada mesin dengan baik.
Penggunaan baja karbon menengah ini biasanya digunakan untuk poros / as, engkol dan sparepart llainnya. c. Baja Karbon Tinggi.
Kandungan karbon pada baja ini antara 0.55 sampai 0.70 % .
Karena kadar karbon yang tinggi maka baja ini lebih mudah dan cepat dikeraskan dari pada yang lainnya dan memiliki kekerasan yang baik, tetapi susah dai bentuk pada mesin dan sangat susah untuk dilas. Penggunaan baja ini untuk pegas/per, dan alat-alat pertanian.
BAJA PADUAN
Sifat mekanis dari baja dapat berubah jika kita menambahkan bahan paduan seperti Mangan, Chrome, Nickel, Wolfram, Silisium, dan lainnya.
Disebut baja paduan jika elemen pemadu yang terkandung didalamnya mencapai 0.8 %.

Semua baja mengandung belerang (S) dan phosphor (P) tapi dalam kadar yang kecil sehingga tidak akan disebut elemen paduan.
Kadar Belerang (S) yang terlalu tinggi akan mengakibatkan baja bersifat rapuh jika dalam kedaan panas.
Kadar Phosphor (P) yang terlalu tinggi akan mengakibatkan baja bersifat rapuh jika dalam kedaan Dingin. 2. Silizium
Silizium (Si) terdapat dalam setiap baja tapi kandungannya kecil, namun baru dapat dikatakan elemen paduan jika kadarnya lebih dari 0.5 %.
Silizium berguna untuk menaikkan kekuatan /batas mulur atau batas plastis. Akibat dari silizium ini baja menjadi berbutir kasar dan berserat dan cocok untuk pegas ( Spring Steel )
Silizium menurunkan kecepatan pendinginan kritis. Baja paduan silizium dapat dikeraskan sampai intinya dengan lebih baik. 3. Mangan
Mangan (Mn) juga terdapat dalam setiap baja tapi kandungannya kecil, namun baru dapat dikatakan elemen paduan jika kadarnya lebih dari 0.6 %.
Semakin tinggi kadar mangan, semakin turun temperature ubah gama-alpha, sehingga baja dengan kadar mangan 1.2 % pada temperarur kamar (20ºC) masih berstruktur austenit. Baja jenis ini sukar dikerjakan tetapi tahan aus.
Kadar mangan yang kecil sudah dapat menurunkan kecepatan pendinginan kritis. Oleh sebab itu baja dengan kadar mangan 1.0 sampai 1.2 % sedah dapat dikeraskan dengan pendinginan / quenching olie ( Baja keras oli ) 4. Chrome
Chrome (Cr) berperan dalam pembentukan carbide . Senyawa carbide ini sangat keras dan dengan sendirinya kekerasan baja akan naik. Adanya senyawa chrome ini menyebabkan besi juga tahan aus.
Chrome juga menyebabkan baja memiliki struktur butiran yang lebih halus, dan chrome juga menyebabkan turunnya kecepatan pendinginan kritis yang sangat besar.
Kadar chrome ddalam besi mulai dari 1.5 % dan dikeraskan dalam oli sampai intinya dengan baik.
Baja dengan kadar chrome diatas 13 % dan kadar karbon kurang dari 0.6 % bersifat anti karat atau disebut juga baja stainless steel. 5. Nickel
Nickel (Ni) menurunkan temperature ubah gamma-alpha dengan cepat. Baja dengan kadar nickel yang tinggi berstruktur austenit. Baja ini anti karat, tahan panas, ketahanan impact dan vatic tinggi tapi tidak dapat dikeraskan.
Baja –Nickel dapat dikeraskan dalam oli dan air. 6. Molybdenum
Molybdenum (Mo) sangat berperan dalam pembentukan carbide. Molybdenum meningkatkan kekuatan,dan batas mulur baja, terutama terhadap pembebanan yang continue dan juga menaikkan temperature tempering.
Baja paduan molybdenum tidak cenderung membentuk struktur butiran yang kasar sehingga lumayan tahan terhadap panas. 7. Wolfram
Baja dengan kadar wolfram 18 % dan carbon 0.7 % sudah bersifat Eutectoid-atas, meskipun sebagian carbon dipakai untuk pembentukan wolfram carbide. Kandungan wolfram tinggi akan menaikkan kekerasan baja dan dengan sendirinya menaikkan kemampuan potong dan tahan aus.
Kecepat6an pendinginan kritis tidak diturunkan secara mencolok oleh wolfram jadi baja ini termasuk baja keras air.
Wolfram memperhalus struktur butiran yang akan menaikkan temperature tempering .
Wolfram dipakai pada HSS dan Hot Work Steel. 8. Vanadium
Pengaruh Vanadium (V) sama seperti Wolfram, tetapi Vanadium memiliki pengaruh yang lebih besar dalam pembentukan carbide, oleh sebab itu dibutuhkan kadar carbon yang tinggi.
Vanadium membuat baja menjadi tahan panas, menaikkan kemampuan potong dan tahan terhadap gesekan. 9. Cobalt
Sebagai elemen paduan Cobalt hanya digunakan jika bersenyawaan dengan elemen lain karena cobalt tidak memiliki pengaruh yang besar terhadap struktur baja.
Cobalt sangat mempengaruhi sifat magnetic dari baja dan berperan pada pembentukan struktur butiran kasar.
Contoh Baja Paduan
• Fe + Ni
Fe + 2 % Ni untuk baja keeling
Fe + 25 % Ni tak bekarat dan tak magnetik
Fe + 36 % Ni baja invar, sifat muai yang sangat kecil
• Fe + Cr
Kuat, Keras, dan Tahan Karat
Fe + Cr > 12 % dinamakan Stainless Steel ( Baja Tahan Karat )
Prosentase yang banyak digunakan adalah :
Fe + 0.1 sampai 0.4 % C + 12 sampai 14 % Cr
Fe + 0.9 sampai 1.0 % C + 17 sampai 19 % Cr
Sifat tahan karat ini disebabkan karena terjadinya lapisan chromoksida (Cr2O3) pada permukaan baja yang menghalangi terjadinya karat. Bila prosentase C terlalu besar maka sifat tahan karat akan menurun karena sebagian Cr akan diikat menjadi CrC. Prosentase ideal adalah C < 0.1 %
• FE + Cr + Ni
Baja tahan asam (acid)
Contoh : baja 18/8 (18 % Cr + 8 % Ni) atau disebut juga baja Crupp
• HSS (High Speed Steel)
Biasa digunakan sebagai alat potong karena memiliki sifat Red Hardness yaitu tetap memiliki kekerasan yang tinggi walaupun temperaturnya mencapai 600 ºC
Contoh:
Fe + 0.7 – 0.8 %C
3.8 – 4.4 %Cr
17.5 – 19 % W
1.0 – 1.4 %V
Fe + 0.85 – 0.95 %C
3.8 – 4.4 %Cr
8.5 – 10.0 %V
2.0 – 2.6 %V
BESI TUANG
Pengelompokan Besi Tuang
Secara umum besi dengan kadar carbon di atas 1.7 % disebut besi tuang, meskipun biasanya besi tuang memiliki kadar carbon 3 – 4.5 %. Besi tuang banyak digunakan dalam dunia tehnik dan industri karena karakteristik atau sifat mach inability yang mudah dikerjakan dengan mesin dan memiliki sifat tahan aus karena bersifat self lubrication, dan tentunya dari segi harga jauh lebih murah dari baja.
Besi tuang dibagi menjadi 2: 1. Besi Tuang Kelabu (Grey Cast Iron)
Sebagian besar dari Zat arang/karbon dalam besi tuang ini terpisah sebagai graphite .
Bidang patahan dari besi tuang ini berwarna abu-abu tua sampai hitam.
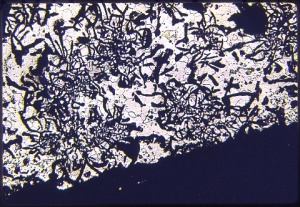
Dimana sebagian besar karbon yang terikat dalam besi sebagai zementite (Fe3C) yang keras.
Besi tuang ini memiliki bidang patahan yang berwarna putih. Sifat yang keras sehingga sukar dikerjakan di mesin.
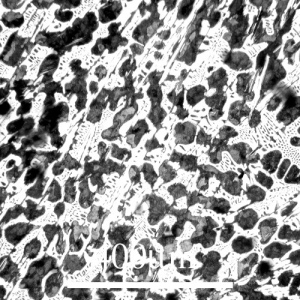
Sifat-sifat dari besi tuang sangat terpengaruh pada unsure-unsur yang ditambahkan pada proses pembuatannya seperti Carbon, silisium, mangan, phosphor, belerang.
Pengaruh dari unsur-unsur diatas akan kita bahas seperti di bawah ini.
PENGARUH UNSUR PADUAN a. Carbon (C)
Bila carbon terikat pada besi tuang sebagai cementite akan diperoleh besi tuang putih, dan bila carbon terikat sebagai graphite akan diperoleh besi tuang kelabu. Dengan adanya graphite besi tuang jadi mudah dikerjakan dengan mesin tetapi kekuatannya berkurang. b. Silisium (Si)
Silisium memperbesar pemisahan graphite sehingga mengurangi kekuatan tarik dan merendahkan titikcair.
Kadar Si terlalu tinggi menyebabkan besi tuang lebih berpori-pori. Kadar Si idealnya 2-3 % c. Mangan (Mn)
Mangan mencegah terjadinya pemisahan graphite sehingga memungkinkan terbentuknya cementite yang keras. Mn membuat besi tuang lebih keras dan memiliki kekuatan tarik yang tinggi. d. Phosphor (P)
Phosphor menghasilkan besi cair yang tipis, lunak, tetapi sangat rapuh. Pada umumnya kadar phosphor lebih kecil dari 1% e. Belerang (S)
Kebalikan dengan phpsphor, belerang menghasilkan besi cair yang tebal dan mempersukar pemisahan graphite.
Kadar belerang umumnya di bawah 0.1 %. Pada kadar 0.2 % pencairan besi cukup tebal sehingga sulit untuk dituang lagi.
BERDASARKAN KEKUATANNYA BESI TUANG KELABU DIBEDAKAN ATAS : a. Besi tuang kekuatan rendah
Memiliki kekuatan tarik 12 – 21 kp/mm2. Biasa digunakan untuk elemen mesin yang tidak terkena beban yang berat.
Komposisinya :
3.2 – 3.6 %C
1.7 – 3.0 % Si
≤ 0.5 % Mn
≤ 0.5 % P
≤ 0.12 % S
Strukturnya berbentuk Ferrite + Graphite atau Pearlite + Ferrite + Graphite b. Besi tuang kekuatan sedang
Memiliki kekuatan tarik sampai dengan 40 kp/mm2. Besi tuang ini biasanya digunakan untuk silinder mesin, piston, dll
Komposisinya :
2.8 – 3.0 % C
1.5 – 1.7 % Si
0.8 – 1.0 % Mn
≤ 0.3 % P
≤ 0.12 % S
Strukturnya berbentuk Pearlite. Pada proses peleburan ditambahkan 10 – 30 % baja bekas unruk mengurangi kadar carbon. c. Besi tuang kekuatan tinggi
Memiliki kekuatan tarik lebih besar dari 40 kp/mm2. Struktur Graphite berbentuk bola sehingga disebut besi tuang modular.
Pada proses pembuatannya besi tuang ini ditambahkan 1.2 % magnesium yang akan menghasilkan graphite yang berbentuk bola pada saat pembekuan, dan juga memperbesar kekuatannya .
BESI TUANG TEMPA (Malleable Cast Iron)
Biasanya besi tuang tidak dapat ditempa, tapi ada jenis besi tuang yang dapat ditempa yaitu besi tuang putih (White Cast Iron),tetapi harus lewat perlakuan khusus yaitu proses Anneling.
Besi tuang putih yang sering digunakan yaitu:
• 1.7-2.8 % C, 1.4-1.6 % Si, 0.4-0.7 % Mn, 0.2 % P, 0.12 % S
• 2.8-3.2 % C, 0.5-0.8 % Si, 0.4-0.7 % Mn, 0.2 % P, 0.12 % S
Proses Anneling a. Ferritic Melleable Iron / Besi Tempa Ferrit
Dengan cara memanaskan besi tuang putih kadar karbon rendah pada suhu 950 – 1000 ºC dalam dapur yang bebas Oksidasi, setelah itu proses pendinginan sampai suhu 740 ºC kemudian didinginkan dengan sangat lambat sampai suhu 680 ºC baru didinginkan di udara.
Pada pemanasan ini akan terlepas dari cementite dan pada pendinginannya karbon akan menghasilkan graphite yang berbentuk bunga, bidang patahan gelap sehingga disebut black heart cast iron. b. Ferrite – Pearlitic Malleable Iron/ Besi tempa Ferrit
Adalah dengan memanaskann besi tuang putih dengan medium oksidasi yaitu bijih – bijih besi selama 60 jam pada suhu 1000 ºC lalu didinginkan. Pada proses ini karbon dari cementite akan dioksidasikan membentuk gas CO2. Pada pemanasan ini semakin lama karbon semakin berkurang dan pada proses pendinginan karbon yang tersisa akan membentuk pearlite dan graphite bunga, bidang patahan gelap sehingga disebut black heart cast iron.
PERLAKUAN PANAS PADA BESI TUANG
Untung menghilangkan tegangan – tegangan dalam pada waktu penuangan besi tuang serta untuk memperbaiki sifat mekanis dan sifat mach inability nya biasanya besi tuang terlebih dahulu harus melalui proses heat treatment . a. Annealing Untuk menghilangkan tegangan dalam
Dengan memanaskan besi tuang sampai suhu 500 – 550 ºC selama 6-8 jam kemudian didinginkan secara perlahan . b. Annealing untuk melunakkan besi tuang
Besi tuang biasanya pada permukaan / kulitnya sangat keras sehingga sangat sulit untuk di kerjakan di mesin karena permukaan besi tuang mengalami proses pendinginan yang lebih cepat dibandingkan pada inti / bagian dalam dari besi tuang, untuk itu perlu proses pelunakan dengan cara memanaskan besi tuang pada suhu 850-900 ºC selama 30 menit sampai 8 jam tergantung dari ketebalan besi tuang yang di annealing, kemudian didinginkan secara perlahan. c. Hardening dan tempering
Besi tuang dipanaskan pada suhu 860 – 900 ºC kemudian di quenching dengan oli atau dengan udara untuk bentuk yang komplex , setelah itu dilakukan annealing pada suhu 200-300 ºC untuk memperbaiki sifat mekanisnya.
Struktur akhir berupa martensit dan graphite.
Tidak ada komentar:
Posting Komentar